
I joke sometimes that we probably break more microphones than some companies sell – just to make sure we’re delivering the best we can.’īecause of this constant refinement, Born admits to having seen more prototypes of TwinPlex capsules than he can pin down to a number. How do you measure that? We’ve been building hundreds of thousands of microphones for the last year just to make sure we’re getting those yields that we need to get. These parts are so tiny, we have a 1mm spacer washer. And, if you’re using bad parts and don’t know you’re using bad parts, you’re going to make bad products. ‘Obviously we don’t want to waste time, we don’t want to waste materials. Anything below about 95% yield and the manufacturing department gets quite skittish,’ explains Born. ‘We have a pretty high standard of manufacturing at Shure. The decades of knowledge and the expertise in Shure’s acoustical lab is just the beginning of the development process, however. We invested pretty heavily in some very expensive measurement and scanning equipment, to make sure that we’re getting good parts, so we’re not going to make bad microphones and not know why.’ When you have a measurement spec of 5μm, we have to be able to measure a single micron just to make sure we’re meeting 5μm. ‘We had to invest pretty heavily in our measurement capabilities. ‘A condenser mic is all about flatness how the parts stack together and how that condenser microphone is formed,’ he adds. The TwinPlex TL46/TL47 subminiature lavalier microphone family It’s a useful illustration of the inherent challenges working at such a small scale brings. The parts are so small that without a magnifying glass, next-to-no detail can be discerned. It’s at this point that Born hands over a small Perspex box containing a set of tiny components that make up the TwinPlex capsule. The mechanical side of TwinPlex was extremely hard.’
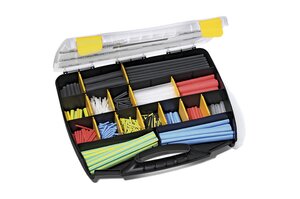
Exploring new suppliers and getting parts from new places was key. The real challenge was – how do we physically make it? And after that, our supply chain – pushing our boundaries on part processes and suppliers. ‘We do a lot of simulations and a lot of modelling that means we can match components together and know that we’re going to get a certain response acoustically. But this gave him the acoustic landscape to throw everything at the microphone that we’d ever dreamed of.’ We looked at 3D printing with the Nest, some crazy backplate PCB manufacturing processes where we’d meld two plates together and a whole load of other techniques. Some of them worked and some of them didn’t. We went down a whole bunch of different routes. Starting from scratch with a new condenser microphone gave him a clean slate, so we could make the backplate any shape we wanted, and we could make the diaphragm any dimension we wanted and from any material. He knew that we wanted to try a lot of new things with TwinPlex that we were not using in our existing models. Jeff had a lot of ideas and he knew a lot about our competitor mics. I work very closely with him and I’m down there every day talking about what we can do, how we can do it better, what ideas we have. ‘Jeff Segoda was the lead acoustical engineer. The idea for the dual-diaphragm capsule was a collective effort that started with a technical development in the acoustic department, notes Born. I’m the product manager for the wired category.’ ‘The way development works at Shure is that we’re divided up into four different segments of product management: wireless, wired, conferencing and software.
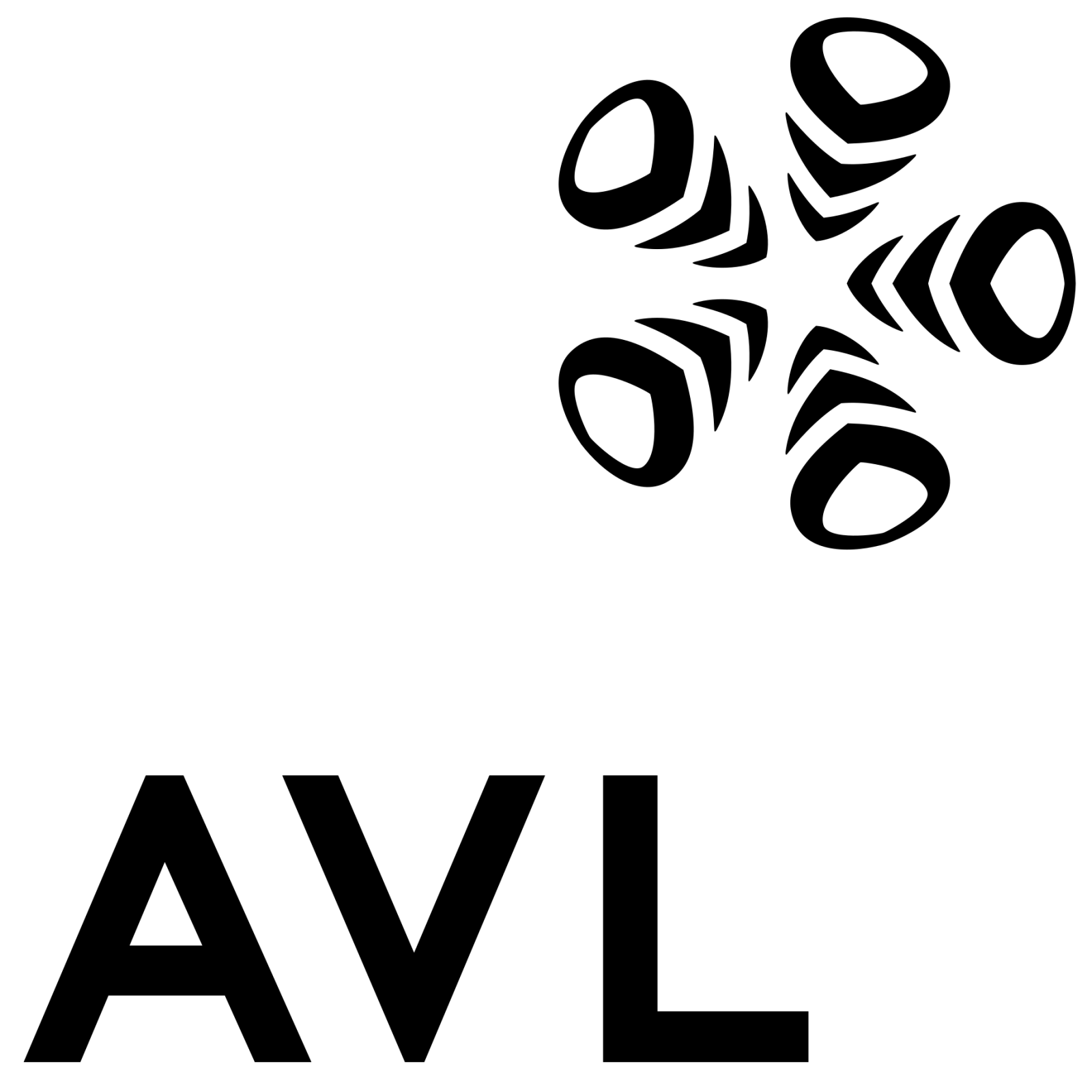
‘It was pretty common knowledge here at Shure that we needed some better lavs and headsets, and the impetus for it was that we knew Axient Digital was going to happen,’ explains John Born, senior global product manager at Shure. The benefits of such a capsule are described by Shure as providing ‘unprecedented’ off-axis consistency, a low noise floor and high SPL, and a ‘natural’ high-frequency response. Like the KSM8, TwinPlex is also home to a dual-diaphragm, omnidirectional capsule, albeit at a fraction of the size.
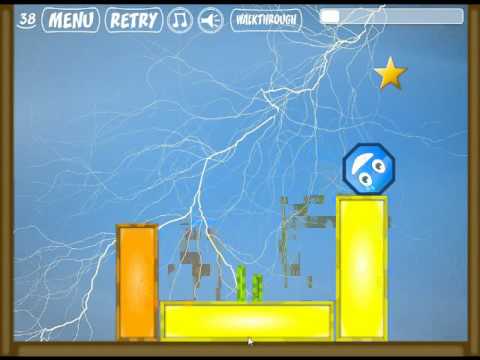
Shure made a big deal about the virtues of its dual-diaphragm technology that first appeared in the KSM8 handheld microphone in 2016. The new line is Shure’s attempt to firmly break into market sectors such as theatre, where there is already no shortage of great solutions on offer. With the manufacturer launching TwinPlex at the NAB Show in April this year, we took a step back to recall a recent visit to the company’s HQ in Chicago to find out more about the development of its new miniature microphone capsule. For a company with the vast heritage of Shure, one that has been designing and manufacturing microphones for nearly a century, what else can there be to learn about mic technology than tailored tweaks here and there to pre-existing and already highly successful models? As it turns out, quite a lot.
